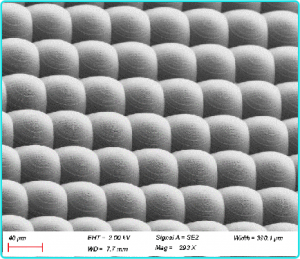
Micro and Nano Processing丨Electron Beam Lithography (EBL) Technology Introduction
What is electron beam lithography?
Electron beam lithography (e-beam lithography; EBL) is a kind of maskless lithography, which uses focused electrons with very short wavelengths to directly act on the surface of the electron-sensitive photoresist (resist) to draw micro and nano structures that match the designed pattern. EBL systems have the advantages of ultra-high resolution (graphic transfer with a limit size of <10 nm) and flexible mapping (direct writing without mask), but due to low exposure efficiency and complex control, EBL is more often used for making lithography masks, advanced principle prototypes and nanoscale scientific research and development.
Development History
- MIT researchers first used electron-induced carbon contamination to form etching masks to produce high-resolution two-dimensional graphic structures in 1958
- 100nm structures were made using electron beam exposure as early as 1965
- PMMA was used as an electron beam photoresist in 1968
- 1970: 0.15um sound surface wave device made with PMMA
- 1972: 60x60nm aluminum metal lines with cross-section on silicon surface using electron beam lithography
In the 1980s, it was widely believed at that time that optical exposure had come to an end and electron beam lithography was the most promising alternative means, however, more than 30 years have passed and electron beam lithography still cannot replace optical exposure. The development of the two lithography technologies has gradually formed a complementary pattern, and it is believed that this pattern will continue to be maintained for a long time.
Theoretical basis
Lithography is the use of light irradiation polymer generated by the changes in the formation of graphics, the resolution of optical exposure is limited by the wavelength of light, in order to improve the resolution of optical exposure, the choice of light wave has undergone the development process from G line to I line, deep ultraviolet, extreme ultraviolet continuously shortened.
The electron beam is essentially a charged particle, and according to the wave-particle duality theory, its wavelength is
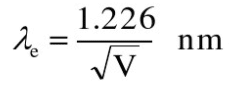
Electron beam exposure system
- The hot electron source is to heat the cathode to a high enough temperature that the electrons in the cathode material can gain enough kinetic energy to enable the electrons to break through the potential barrier of the electron gun metal work function and be emitted to form an electron beam.
- The field emission source is formed by strengthening the electric field, which makes electrons tunnel through the potential barrier to form the electron source. The focusing and deflection of the electron beam from the electron emitting source is done in the electron beam column, which consists of a series of electron lenses, diaphragms, baffles and other devices. The electrons are shaped by the diaphragm, converge into a beam spot by the electron lens, and are exposed on the bench by the deflection system.
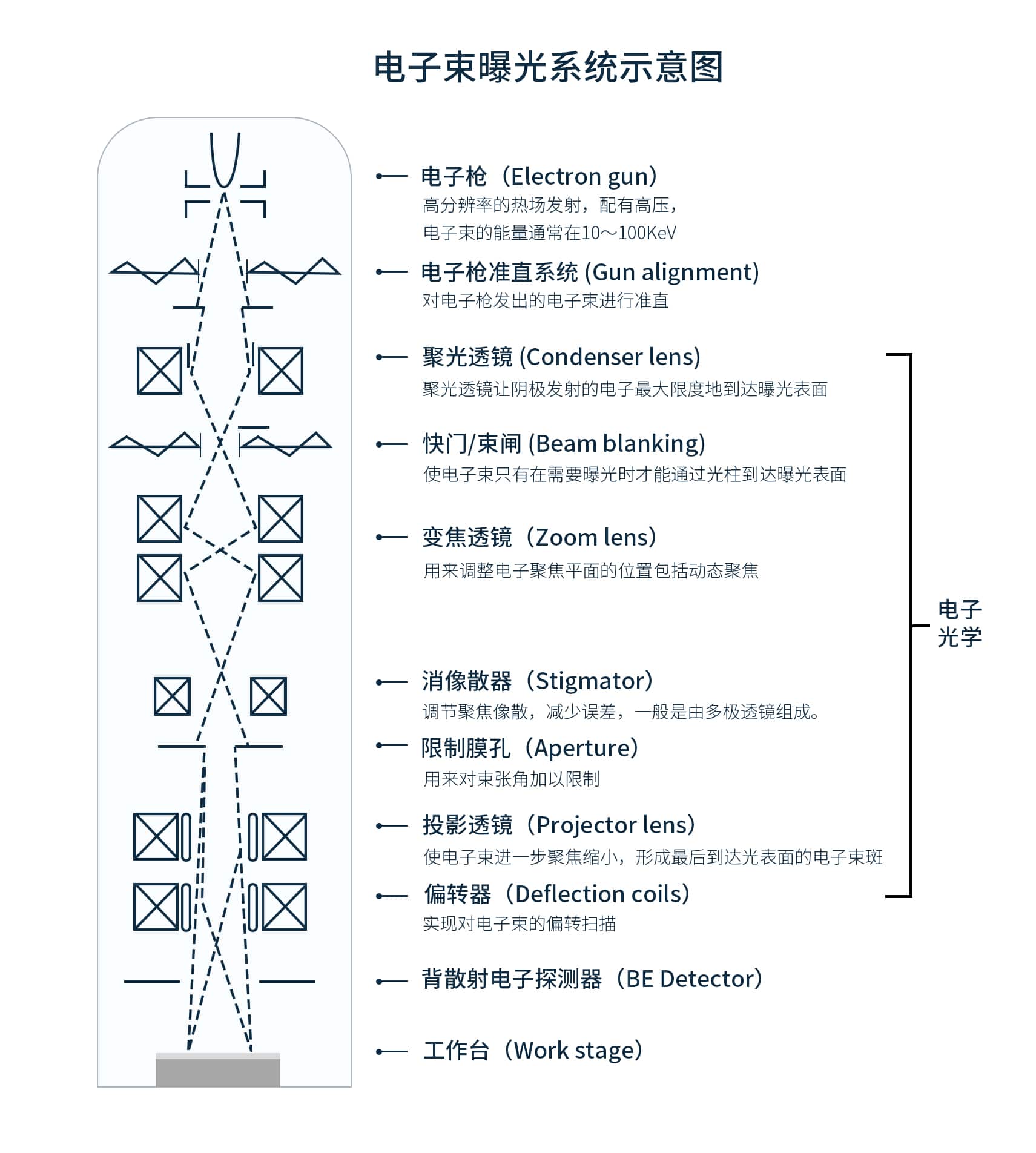
Important indicators for electron beam exposure systems
- Minimum bundle diameter.directly affects the minimum size of the exposure pattern. Smaller spot diameters can be obtained by adjusting the following measures: ① setting the acceleration voltage as high as possible ② using a smaller size diaphragm aperture ③ using a smaller working distance ④ setting a smaller scanning field ⑤ setting a smaller exposure step
- Acceleration voltage.Generally, the higher the acceleration voltage of 10~100kv, the higher the resolution, the smaller the proximity effect produced by the exposure, and the thicker the resist can be exposed.
- Electron beam flow.The larger the beam current the faster the exposure speed, the maximum exposure speed is limited by the scanning frequency, the beam spot of large beam current will also be larger
- Scanning speed.The faster the scan speed the faster the exposure speed, expressed in terms of frequency (e.g.: 50MHz)
- Scanning field size.Scanning field is large, the majority of the exposed graphics can be exposed in the scanning field to avoid errors caused by the stitching of the scanning field
- There are also table movement accuracy, registration accuracy, field splicing accuracy, etc.
Electron beam exposure method classification
Classified by working mode
Projection exposure (mask required) and direct exposure (no mask required)

Divided by scanning method
Divided into raster scan (raster scan) and vector scan (vector scan)
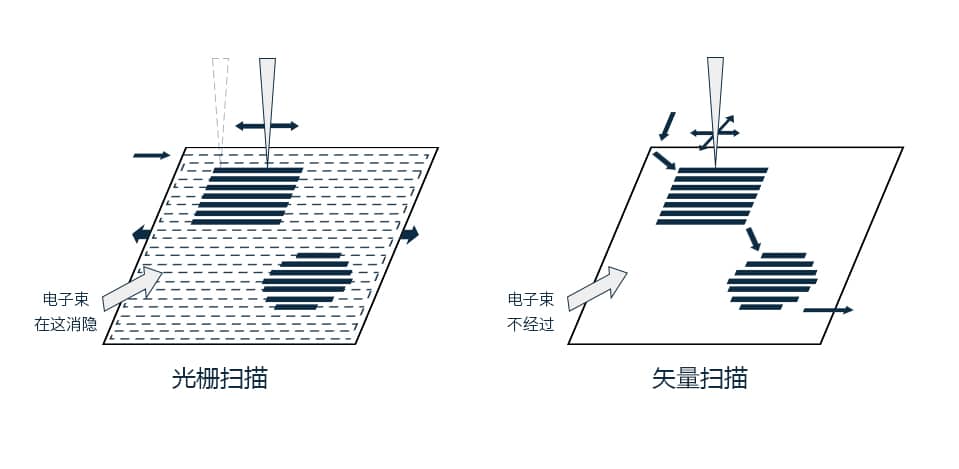
- Raster scanningThe Gaussian circular beam is used, and the electron beam is scanned continuously point by point throughout the scanning field, and the exposure of the image is performed by controlling the shutter (beam gate) on and off.The advantages of raster scanning are simple control and no control of the deflection system is required. The disadvantage is low production efficiency. Because of the small scanning field, the exposure must be done in conjunction with the movement of the workpiece table.
- Vector scanThe advantages of vector scanning are high exposure efficiency, scanning exposure only in the graphic area, reducing the time spent by the lens in non-graphic areas, and the possibility of using a variable rectangular beam. The disadvantage is the complexity of the control system, because vector scanning must control the deflector, unlike raster scanning with a fixed deflection.
According to the electron beam shape is divided into
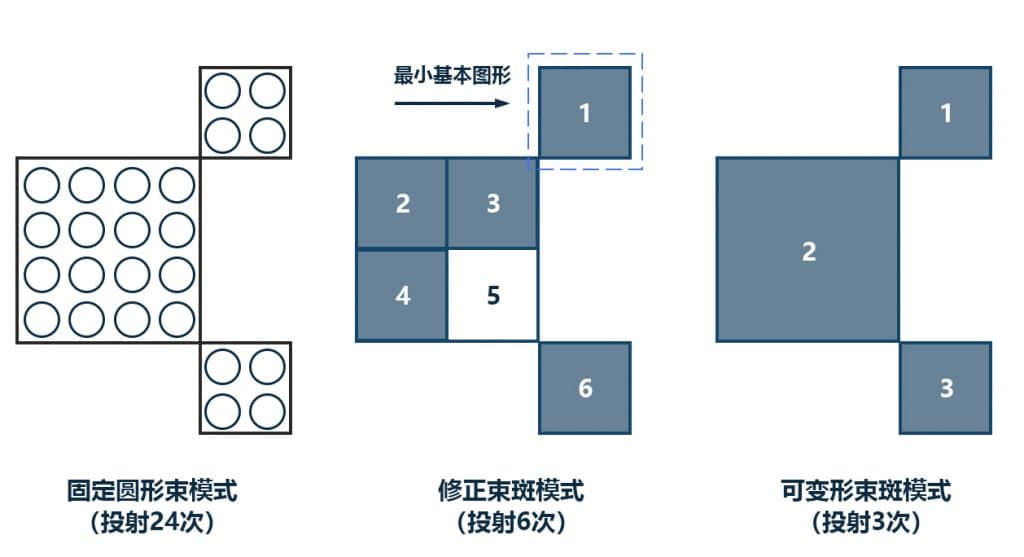
In vector scanning mode, the exposure time of the pattern is related to the number of beam spot projections.In the fixed Gaussian beam (circular beam) spot mode, we need to perform 24 projections.
To speed up the exposure rate, the pattern can be decomposed into a combination of the smallest basic pattern, using the smallest basic pattern as the shape of the electron beam spot. Only 6 projections are required in this corrected beam spot mode.
However, in the real production process the pattern is not constant and the basic beam spot shape needs to be reset frequently, so a more flexible projection method is needed. A variable beam spot mode can be applied to the case of diverse patterns. As shown in the figure below, in the variable beam pattern mode, the electron beam spot can be adjusted to the specific pattern, changing the basic beam spot shape and reducing the number of projections to three.
Introduction to Electron Beam Photoresists
Photoresist (Photoresist; also known as photoresist ) is an etch-resistant film material whose solubility is changed by irradiation or radiation from light sources such as ultraviolet light, excimer laser, electron beam, ion beam, and X-ray.
Electron beam photoresists are usually divided into positive and negative photoresists, can be divided according to who dominates the cross-linking reaction or chemical bond breakage after photoresist irradiation.Photoresist positive and negative characteristics are not absolute, for example, electron beam positive adhesive PMMA at 10 times the normal exposure dose, the adhesive in the exposed area carbonizes, resulting in residuals during development, and its properties can be used as a negative adhesive.
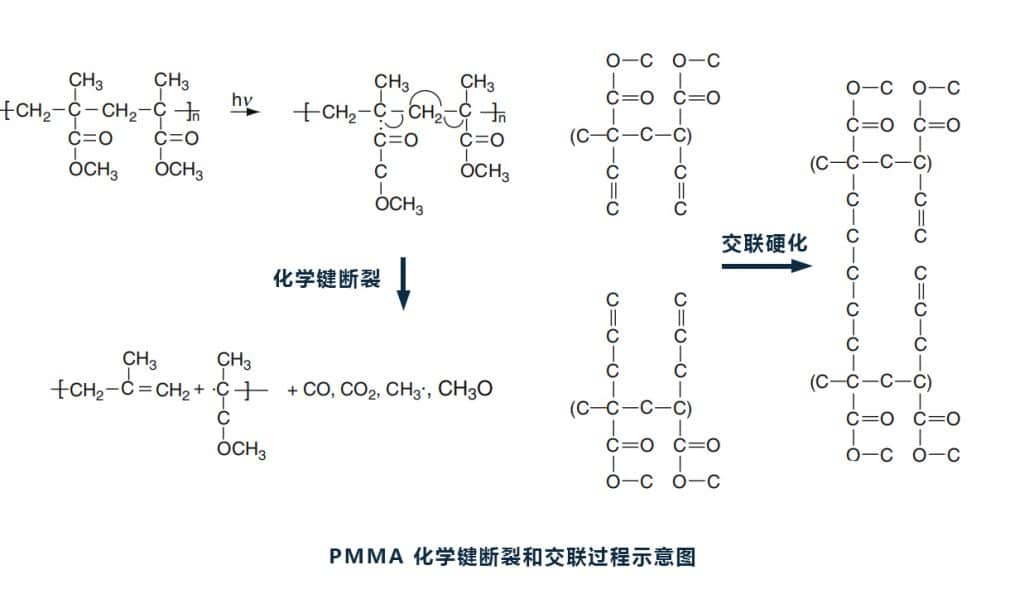
Positive photoresist (positive adhesive): the chemical bond breaking reaction in the photoresist in the exposure area dominates and is easily soluble in the developing solution.
Negative photoresist (negative adhesive): the cross-linking reaction in the photoresist in the exposure area is dominant, from small molecules cross-linked polymerization to large molecules, difficult to dissolve in the developing solution.
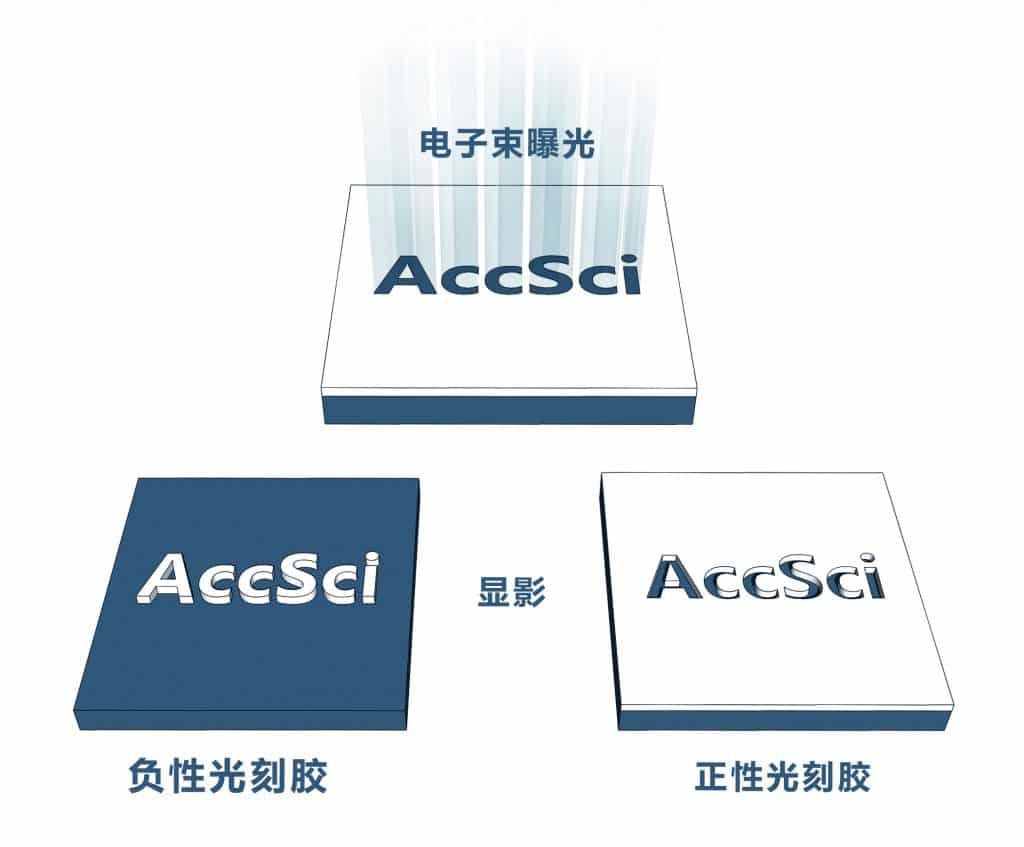
Key parameters of photoresists
Similar to UV photoresists, we usually select or evaluate a photoresist for process application by the following four parameters: sensitivity, contrast, resolution, and etch resistance.
- Sensitivity.The higher the sensitivity of the photoresist, the smaller the exposure dose (irradiation) required. The sensitivity is affected by the electron capacity keV (or acceleration voltage kV), substrate material, process conditions, developer used and other factors
- Contrast ratio.High contrast yields steeper sidewalls, greater processing headroom, better resolution, higher aspect ratio structure, making it less sensitive to proximity effects and higher pattern density. Low contrast is only applicable to 3D grayscale lithography
- Resolution.defines the size of the smallest feature that can be obtained or the minimum distance between two structures.
- Etching resistance.If the subsequent etching process is required, a photoresist that can maintain its integrity during chemical (wet) and physical (dry) etching should be selected.
In addition, it is necessary to consider the selection of suitable photoresist in combination with the positive and negative characteristics of photoresist, process tolerance, adhesion, thermal fluidity, expansion effect, storage life and other parameters.
Commonly used photoresists
Different photoresists are required for different applications, and this section introduces the concentrated electron beam photoresists commonly used in experiments, including positive PMMA, ZEP-520A, AR-P 6200 (SCAR62) and negative HSQ.
PMMA (ortho-glue)
PMMA (poly-methyl methacrylate), a polymer, also known as acrylic or plexiglass, is currently the most popular electron beam photoresist. 5%~10% PMMA powder and chlorobenzene or anisole (less toxic, 2-4%) can be fully mixed to make PMMA photoresist.
- Cheap, durable, easy to operate
- Very high resolution and contrast
- Low sensitivity
- Poor dry etching resistance (good for peel lift-off, not suitable for direct etching pattern transfer)
- The sensitivity increases as the relative molecular mass decreases, and the typical relative molecular masses of PMMA are 495 kg/mol and 950 kg/mo
- Contrast and sensitivity can be modulated by changing the ratio of MIBK in the developer mixture (MIBK:IPA). Sensitivity increases with the ratio of MIBK in the developer, while contrast increases in the opposite direction.
Zep-520A (positive rubber)
Zep-520A, the most popular commercial photoresist, was developed by Nippon Zeon in Japan as a PMMA plus benzene ring modified adhesive consisting of a copolymer of α-chloromethacrylate and α-methylstyrene to replace PMMA.
- High resolution and high contrast, with high resolution comparable to PMMA (10-30nm graphic structure achievable) and high contrast
- High sensitivity, with PMMA higher sensitivity (3~5 times)
- High dry etching resistance, more than 5 times compared to PMMA.
- Expensive, with a one-year shelf life.
- For ultra-high sorting rates (sub-10nm), it may be better to use PMMA.
- ZEP-520A is not easy to remove after exposure, development and baking of firm film, usually ZDMAC is used to remove glue
AR-P 6200 (CSAR62) (positive rubber)
- Ultra-high resolution (<10nm)
- High sensitivity, sensitivity can be adjusted by selecting the appropriate developer.
- High contrast ratio (>15)
- High depth to width ratio (up to 20:1)
- Good process stability and resistance to dry etching, which is twice that of PMMA.
- Good adhesion with the substrate, not easy to occur the phenomenon of debonding and cracking.
- Low Young's modulus, prone to collapse, adhesion and overturning.
- Lower melting point, which produces resist melting.
- Graphical surfaces are prone to shrinkage
HSQ (negative glue)
- Very high resolution (<10nm)
- Low sensitivity and long exposure times.
- Development by chemical reaction (reaction of unexposed HSQ with diluted NH4OH or NaOH developer to produce H2), not by dissolution, with good process stability after development.
- Good performance in electron microscopy observation without gold plating.
- A good mask material for etching silicon.
- The shelf life is short, with a storage period of only 6 months. HSQ (H-SiOx) in powder form will have a longer shelf life
- Storage conditions are harsh, the gel is easily oxidized when exposed to air, and the phenomenon of jelly curing occurs, which requires low temperature (5℃) sealed storage.
- Very high contrast, easy preparation of structures with steep and straight profiles and high aspect ratios.
- A stretchable photoresist with good verticality of line edges after development.
- Good adhesion, toughness and non-breakability.
Proximity effect
The proximity effect of electron beam exposure, is when two exposure patterns are close to each other, due to the scattering of electrons in the photoresist and substrate so that the electrons deviate from the original direction of incidence, resulting in the original should not be exposed to the neighboring areas were exposed, and some should be exposed to the region and not enough exposure, resulting in distortion of the exposure pattern. Bring contrast reduction, resolution degradation and other problems.
Correction method
- Dose correctionThe most common application, the best results of a method, the principle is to make all the exposure of artificial graphics are uniform and consistent exposure energy.The dose correction is also divided into: self-consistent technique (physical correction) and geometric cut method.Self-consistent technology (physical correction): relatively accurate, but computationally intensive for large-scale integrated circuit designs.Geometric cut method: the calculated exposure dose distribution is coarse, but the calculation is very fast.
- Graphic size compensationIt compensates for the effects of too high or too low local energy by reducing or increasing the size of each graph, and is suitable for graphs with simple cycle repetition.
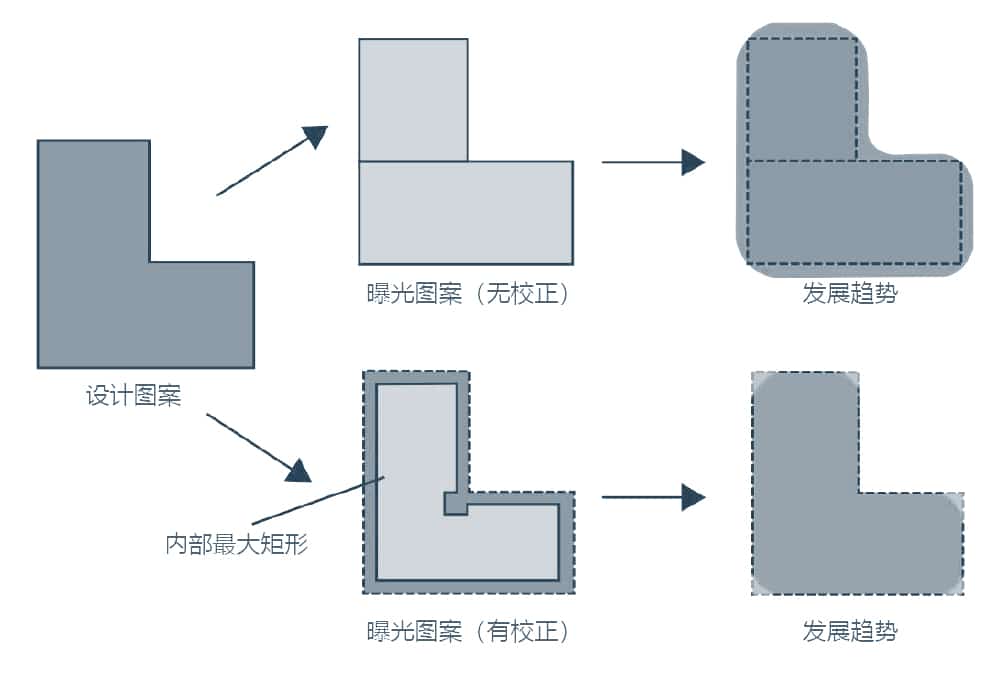
Background Exposure CompensationThe second exposure energy superimposed so that the energy distribution in all parts of the equalization, without the need to calculate the energy distribution, but may make the contrast of the exposure of the image is reduced, suitable for raster scanning exposure system.
The simplest and most effective way to reduce the proximity effect is to increase the electron beam energy and reduce the thickness of the electron beam photoresist.However, it should be considered that high electron beam energy may cause damage and overheating to the substrate.
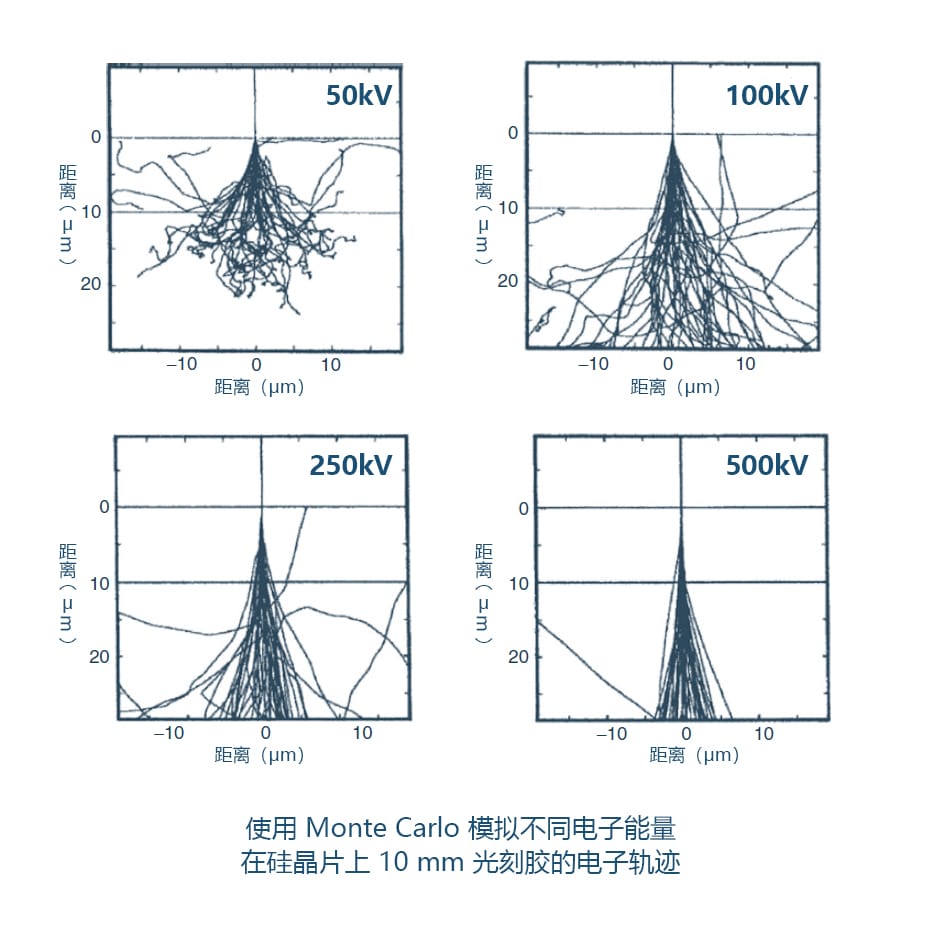
Applications
High-precision mask: Electron beam lithography has a wide range of applications in the field of high-precision mask manufacturing for integrated circuits due to its high resolution and direct writing type.
Optoelectronic field, such as electronic and optoelectronic chip prototyping and small batch production, diffraction grating, binary optics, micro and nano optics (micro lens array, optical waveguide) and super surface lens and other industries of small batch production, special optoelectronic devices customization.
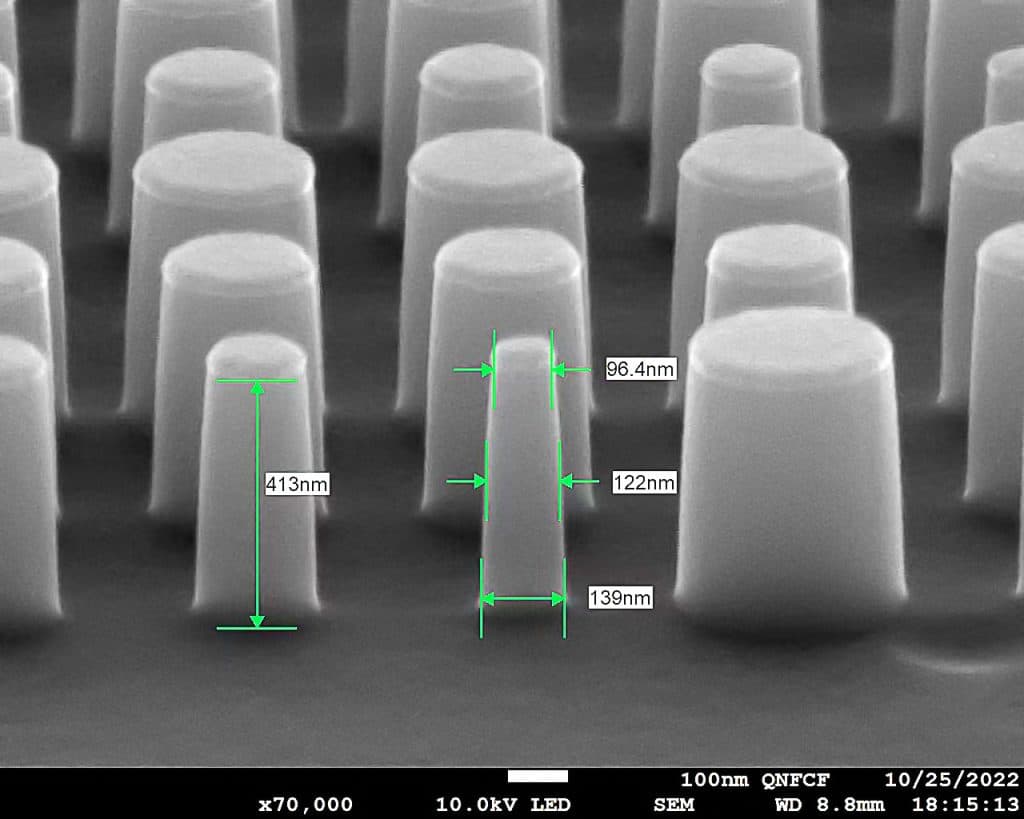
We offer Electron beam lithography / micro and nanostructure processing design services, Feel free to leave a message to inquire.
Micro-Nano Processing | Introduction to Electroplating Process
Micro-Nano Processing | Introduction to Electroplating Electroplating is the use of electrolytic principle to make gold
Micro and Nano Processing | Thin Film Preparation - Epitaxy
Thin Film Preparation - Epitaxy Most materials are amorphous, crystalline or polycrystalline in shape.
Micro and Nano Processing | E-paper micro-cups and micro-chamber structure preparation
Microfabrication | E-paper microcups microchamber type structure preparation For when