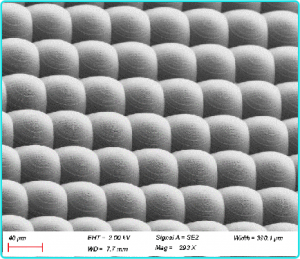
Introduction to Physical Vapor Deposition (PVD) types, characteristics and applications
Catalog
What is Physical Vapor Deposition (PVD)?
Physical vapor deposition (PVD) is a technique that uses physical methods under vacuum conditions to vaporize the surface of solid or liquid materials into gaseous atoms, molecules or partially ionized into ions, and to deposit thin films with a particular function on the surface of the substrate through a low-pressure gas (or plasma) process.
Physical vapor deposition technology can not only deposit metal film, alloy film, but also compound, ceramic, semiconductor, polymer film, etc. It is a new material manufacturing technology with wide application prospect. The super hard film prepared by this technology is not only super hard, but also ultra-thin, high temperature resistant, non-polluting and almost zero emission, which is suitable for the special performance requirements of wear resistance, oxidation resistance, anti-corrosion and self-lubrication on the surface of tools, parts and friction and wear parts, and is one of the most promising and valuable technologies in modern surface engineering.
Physical Vapor Deposition Types
PVD | Advantages | Disadvantages | Applications |
Vacuum Vapor Deposition | ● Simple principle, easy operation, easy control of deposition parameters ● High film purity for thin film property studies ● Fast deposition rate and high efficiency, multiple blocks can be vaporized simultaneously ● More applicable materials ● It is the lowest cost among PVD processes | Relatively poor film-to-substrate adhesion and less than ideal process repeatability | Vacuum vapor deposition is used for optical interference coating of high and low refractive index materials, mirror coating, decorative coating, permeation barrier film on soft packaging materials, conductive film, anti-corrosion coating, etc. When depositing metals, vacuum vapor deposition is sometimes called vacuum metallization. |
Sputtering Deposition | ● Good film-substrate adhesion ● High film purity ● Good denseness, no air holes ● Applicable to most solid materials (especially materials with high melting points), with a wide range of material applications ● Good controllability and repeatability of the sputtering process for industrial production | ● Complex equipment and difficult to control deposition parameters ● Low deposition rate ● Deposition directionality is not as good as vacuum vapor deposition ● Sputtering targets are usually more expensive ● Careful control of gas composition is required during sputtering deposition to prevent target poisoning | Sputter deposition is widely used to deposit thin film metallization on semiconductor materials, coatings on architectural glass, reflective coatings on polymers, magnetic films for storage media, transparent conductive films on glass and flexible webs, dry film lubricants, wear resistant coatings on tools and decorative coatings. |
Ion plating | ● Good film-substrate adhesion ● High denseness ● Good abrasion and corrosion resistance ● Wide range of material applications | ● There are many processing variables to control ● It is often difficult to obtain uniform ion bombardment on the substrate surface, resulting in changes in film properties ● Substrate may be overheated ● Bombardment gas may be incorporated into the growing film | Ion plating is used to deposit hard coatings of composite materials, adhered metal coatings, high density optical coatings and conformal coatings on complex surfaces. The use of ion plating to deposit aluminum films on aerospace components is called ion vapor deposition. |
Vacuum Vapor Deposition
Vacuum evaporation coating is the most common and widespread method in thin film preparation. The principle is to use the heat provided by the outside world to make the film material (thin film material) liquefy by heat and then vaporize, or directly vaporize into a gaseous state and deposit it onto the substrate to form a thin film under vacuum. According to the source of heat, it is divided into: resistance evaporation plating, electron beam (EB)-coating, pulsed laser deposition (PLD), induction heating evaporation plating (Induction- heatedevaporation), etc.
Sputtering Deposition
It is a coating technology that generates ions (Ar) by gas discharge under vacuum conditions and uses positively charged fluorine ions to bombard a solid target with negative potential, so that the target atoms are sputtered out and deposited onto the substrate surface to form a thin film. Vacuum sputtering coating is classified according to different sputtering devices: dipole, tripole or quadrupole sputtering, DC or RF wireMagnetron sputteringThe most widely used are magnetron sputtering, reaction sputtering, ion beam sputtering, etc. Among them, magnetron sputtering is widely used, including DC planar magnetron sputtering, columnar target magnetron sputtering, non-equilibrium magnetron sputtering, pulsed DC magnetron sputtering, RF magnetron sputtering and medium frequency magnetron sputtering, etc.
Ion plating
Ion plating is one of the fastest growing and most widely used coating technologies. The film material (thin film material) is changed from a solid state to a gaseous state in the same way as evaporation plating or as sputtering plating, but the gaseous film material participates in a glow discharge with the working gas during the subsequent transport process and is partially dissociated into ions and electrons, which are deposited onto the negatively charged substrate to form a thin film.Ion plating can be basically divided into three main categories: plasma ion plating (ion plating), arc vapor deposition (arc vapor deposition) and beam ion plating (ion beam deposition).The most typical features that distinguish ion plating from evaporation and sputtering plating are: (i) in ion plating, the atoms of the vaporized film material undergo a dissociation process, and (ii) in ion plating, the substrate is usually subjected to negative bias. Coatings that meet these two conditions can basically be classified as ion plating.
Common Applications
The range of physical vapor deposition (PVD) applications is increasing. Thin films are usually classified into different categories.
- Color PVD coating--Enhancing the durability, beauty and value of products
- High Performance Coating--Heat/cold/pressure/scale/corrosion resistance, biocompatibility
- Diamond-like carbon--Maximize durability, reduce friction or improve appearance
- PVD Chrome Plating Alternatives An attractive, durable and safe alternative to hard chrome
- Copper coating--Copper can be used for its unique appearance and antimicrobial properties
Household products.Coated with PVD film for color change and durability. Faucets may also include internal water metering valves coated with PVD diamond-like carbon layer (DLC) film for long-lasting performance.
Automobile.PVD coatings allow engine parts and drivetrain components to last longer, due to lower friction, higher operating efficiency, high temperature and corrosion resistance. Coatings for internal combustion engines, drivetrain components of ICE/EV vehicles and interior/exterior trim parts.
Medical equipment.Medical devices require properties not found in substrates, such as excellent hardness and toughness, biocompatibility, low coefficient of friction, and compatibility with cleaning agents and other solvents. For orthopedic implants, surgical instruments, dental implants, etc.
We offer Physical Vapor Deposition / Micro and Nanostructure Processing Design Services, Feel free to leave a message to inquire.
Related Products
Related Reading
Micro and Nano Processing | Preparation of Micro and Nano Optical Components
Micro and Nano Processing | Preparation of Micro and Nano Optical Components Micro and Nano optical components are surface
Micro and Nano Processing | MEMS Fine Processing (VI)
Micro and Nano Processing | MEMS Fine Processing 1.6 Sacrificial Layer Technology
Micro and Nano Processing | Introduction to Dry Etching
Micro and Nano Processing | Dry Etching Process Introduction Etching technology is divided into: wet process