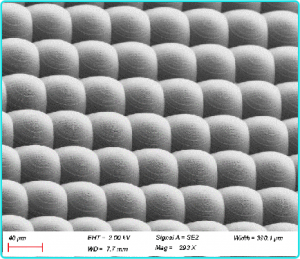
Micro-Nano Processing | Introduction to Wet Cleaning Process
The IC manufacturing process requires the participation of some organic and inorganic reagents to complete, in addition, the manufacturing process is always carried out in a clean room with human participation, so that various environmental contamination of silicon wafers is inevitable. Depending on the occurrence of contaminants, they can be broadly classified as particles, organic matter, metal contaminants and oxides. Wafer cleaning is the most important and frequent step in semiconductor device manufacturing, and its efficiency will directly affect the yield, performance and reliability of the device. Wet cleaning refers to the use of a variety of chemical reagents and adsorption on the surface of the object to be cleaned impurities and oil chemical reaction or dissolution, or accompanied by ultrasound, heating, vacuum and other physical measures, so that the impurities from the surface of the object to be removed from the desorption (desorption), and then rinsed with a large amount of high purity deionized water, so as to obtain a clean surface process. According to the purpose and requirements of silicon wafer cleaning to select the appropriate reagents and washing solution is the first step of wet chemical cleaning.
- The nature and role of common reagents
Category | Commonly used reagents | Nature or role |
---|---|---|
Inorganic acids and bases | Hydrochloric acid, sulfuric acid, nitric acid, hydrofluoric acid, aqua regia, ammonia, potassium hydroxide, sodium hydroxide, etc. | Removal of photopolymer or impurities by chemical reaction |
Oxidizing agent | Nitric acid, concentrated sulfuric acid, potassium dichromate, hydrogen peroxide, etc. | Oxidation |
Complexing agent | Hydrochloric acid, hydrofluoric acid, ammonium chloride, ammonia, etc. | Complexation, which facilitates the removal of metal impurities |
Organic solvents | Anhydrous ethanol, acetone, isopropanol | Similarity solubility principle to remove organic impurities or photo-gel |
Synthetic detergent | The main component is surfactant | Surface active emulsification |
- Inorganic cleaning of silicon wafers
Solution | Temperature | Purpose |
---|---|---|
Sulfuric acid: hydrogen peroxide (3:1) | 120°C - 140°C | Removal of organic matter |
Ammonia: hydrogen peroxide: water (1:1:5) | 75℃ | Removal of particles |
Hydrochloric acid: hydrogen peroxide: water (1:1:7) | 75℃ | Removal of metal impurities |
BHF or BOE | room temperature | Removal of natural oxide layer from silicon wafers |
- Organic cleaning of silicon wafers.
Solution | Temperature | Dissolution performance |
---|---|---|
Acetone | room temperature | Strongest |
Isopropyl alcohol | room temperature | Stronger |
Anhydrous ethanol | room temperature | weaker |
- RCACleaning
The RCA cleaning method relies on solvents, acids, surfactants and water to clean the wafer without destroying its surface characteristics by jetting, purging, oxidizing, etching and dissolving wafer surface contaminants, organic matter and metal ion contamination. After each use of chemical reagents are thoroughly cleaned in ultrapure water. The following are commonly used cleaning solutions and their functions.
(1) Ammonium hydroxide (ammonia) / hydrogen peroxide (hydrogen peroxide) / DI water (deionized water) mixture (APM; NH4OH/H2O2/ H2O at 65~80℃).APM is usually called SC1 cleaning solution, its formula is: NH4OH:H2O2:H2O= 1:1:5 ~ 1:2:7, to oxidation and micro-etching to undercut and remove surface particles; can also remove minor organic contaminants and some metallization contaminants. However, the simultaneous occurrence of silicon oxidation and etching will increase the surface roughness.
APM cleaning with additional megasonic energy can reduce the consumption of chemicals and DI water, shorten the etching time of the wafer in the cleaning solution, reduce the anisotropic effect of wet cleaning on the characteristics of the integrated circuit, and increase the service life of the cleaning solution.
(2) Hydrochloric acid (hydrochloric acid) / hydrogen peroxide (hydrogen peroxide) / DI water (deionized water) mixture (HPM; HCI/ H2O2/ H2O at 65~80℃). ~HPM is usually called SC2 cleaning solution with the formula of HCI: H2O2:H2O=1:1:6, which can dissolve alkali metal ions and hydroxides of aluminum, iron and magnesium, in addition, chloride ions in hydrochloric acid and residual metal ions to form complexes that are easily soluble in aqueous solution, which can remove metal contaminants from the bottom layer of silicon.
(3) Sulphuric acid (sulfuric acid) / hydrogen peroxide (hydrogen peroxide) mixture (SPM; H2SO4/ H2O2 at 100 ~ 130 ℃). SPM is often called SC3 cleaning fluid, sulfuric acid and hydrogen peroxide volume ratio is 3:1, is typically used to remove organic contaminants cleaning fluid. Sulfuric acid dehydrates and carbonizes the organic material, while hydrogen peroxide oxidizes the carbonized products to carbon monoxide or carbon dioxide gas.
(4) Hydrofluoric acid (hydrofluoric acid) or diluted hydrofluoric acid (HF or DHF at 20~25℃) etching. Its formula is: HF:H2O=1:20 or 1:50, mainly used for removing oxides from special areas, etching silicon dioxide and silicon oxides, and reducing surface metals. Dilute aqueous hydrofluoric acid solution is used to remove the native oxide layer and a layer of chemical oxide layer generated by the oxidation of peroxide on the wafer surface after SC1 and SC2 solution cleaning, which also forms silicon hydrogen bonds on the silicon wafer surface while removing the oxide layer, while presenting a hydrophobic surface.
(5) Ultrapure water (UPW) is often called DI water. UPW uses ozonated water to dilute residual chemicals and rinse solution for wafers after chemical cleaning.
Extended Reading.
- Micro and Nano Processing | Overview
- Micro and Nano Processing | Photolithography - Nanoimprint Lithography
- Micro and Nano Processing | Lithography - Focus on Ion Beam FIB
- Micro and Nano Processing | Lithography - Electron Beam Lithography
- Micro and Nano Processing | Photolithography - Optical Lithography
- Micro and Nano Processing | Etching
- Micro- and Nanofabrication | Thin Film Preparation - Epitaxy
- Micro and Nano Processing | Thin Film Preparation - PVD
- Micro and Nano Processing | Thin Film Preparation - CVD
We offer fastMEMS device / micro and nanostructure processing design services, Feel free to leave a message to inquire.