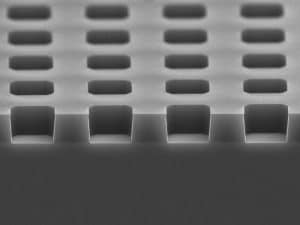
Micro and Nano Processing | Introduction to Thin Film Deposition Process
What is thin film deposition (coating)?
Comparison of thin film deposition process types and advantages and disadvantages
Physical vapor deposition (PVD) is a method of growing thin films on a substrate by heating the source material under vacuum to allow atoms or molecules to escape from the surface of the source material.The main methods of physical vapor deposition are vacuum electron beam or resistance vapor deposition, sputtering coating, arc plasma coating, ion coating, and molecular beam epitaxy, etc. The electron beam evaporation system and sputtering system of AEMD are both physical vapor deposition.
ThingsPhysical Vapor Deposition (PVD) can be divided into two main categories, thermal evaporation deposition and plasma sputtering deposition.Thermal evaporation deposition:Resistance evaporation deposition, ,Electron beam evaporation deposition;.Plasma sputtering deposition: TheDC sputtering, RF sputtering, magnetron sputtering, ionized PVD.
Chemical Vapor Deposition (CVD) is a process that causes a gaseous substance to react chemically on the surface of a solid and deposit on that surface to form a stable solid film.There are four main important stages: 1) diffusion of the reaction gas to the substrate surface; 2) adsorption of the reaction gas to the substrate surface; 3) detachment of the gas phase by-products generated on the substrate surface from the surface; and 4) formation of a cladding layer from the reactants left behind. The use of techniques such as plasma and laser assistance can significantly facilitate the chemical reactions so that deposition can take place at lower temperatures.
Chemical Vapor Deposition (CVD)Including low pressure type (LPCVD), atmospheric pressure type (APCVD), atomic layer deposition (ALD), plasma enhanced type (PECVD) and metal organic compound type (MOCVD), etc.
Atomic Layer Deposition (ALD)It is a type of chemical vapor deposition (CVD) method, which is a method that allows a substance to be plated on the surface of a substrate in the form of a single atomic film layer by layer. Atomic layer deposition has similarities with ordinary chemical deposition. However, during atomic layer deposition, the chemical reaction of a new layer of atomic film is directly associated with the previous layer, allowing this method to deposit only one layer of atoms per reaction.
Comparison of the advantages and disadvantages of various thin film deposition methods
Craftsmanship | Atomic layer deposition (ALD) | Physical Vapor Deposition (PVD) | Chemical Vapor Deposition (CVD) | Low Pressure Chemical Vapor Deposition (LPCVD furnace tube) |
---|---|---|---|---|
Deposition principle | Chemical surface saturation Reaction-Deposition | Evaporation-Consolidation | Gas phase reaction - deposition | Low Pressure Chemical Vapor Deposition (Stove and tube type) |
Deposition process | Laminar growth | Nucleation growth | Nucleation growth | Nucleation growth |
Step coverage | Excellent | General | Good | Good |
Deposition rate | slow | Quick | Quick | slower |
Deposition temperature | Low(<500℃) | Low | High | Higher |
Uniformity | Excellent 0.07 - 0.1nm | General About 5nm | better 0.5 - 2nm | Better |
Thickness control | Number of reaction cycles | Deposition time | Deposition time Gas phase partial pressure | Deposition time Gas ratio |
Ingredients | Uniformity with few impurities | No impurities | Easy to contain impurities | No impurities |
Film types and application scenarios
Film Type | Classification | Thin film deposition materials | Applications |
Semiconductors | Polysilicon | SiH4 (silane) | Gates of MOS, high value resistors, etc. |
Monocrystalline silicon | SiH₂Cl₂(Dichlorosilane; DCS) | Single crystal epitaxial layer for power devices, etc. | |
SiHCl3 (trichlorosilane; TCS) | |||
SiCl4 (Silicon chloride; Siltet) | |||
Amorphous Silicon | SiH4 (silane) | Alpha-Si solar cell, source/drain trench area, etc. | |
Dielectric quality | Si02 (silicon dioxide) | SiH4, O2 SiH4, N20 Si(OC2H5)4 (tetraethoxysilane), O2/O3 | Most widely used dielectric films, STI, gate oxide, sidewall, PMD, IMD, barrier, hard mask, etc. |
Si3N4/SiN (Silicon Nitride) | SiH4, N2O, N2, NH3 C8H22N2Si [ Bis(tert-butylamino)silane ] | Etch stop layer, hard mask, passivation layer, etc. | |
SiON (Silicon Nitride) | SiH4, N2O, N2, NH3 | Anti-reflective layer, oxide layer, hard mask, etc. | |
PSG/BPSG (Phosphorsilicate / Borosilicate glass) | Silane, borane, phosphorane, etc. | PMD, passivation layer, etc. | |
Low- K (low dielectric) materials | Polyimide (PI), etc. | Replacement of SiO2 in PMD | |
High-K (high dielectric) materials | Hf, O2, SiO2, etc. | Replacement of SiO2 in the grid media layer | |
Metal Metal compounds | W (Tungsten) | WF6 (tungsten hexafluoride), SiH4, H2 | Electrical films, optical films, hard films, corrosion-resistant films, contact holes, through-holes, gates, etc. |
WSi2/TiSi2 /CoSix/NiSi | WF6, silane, etc. | Silicide layer on source/drain/gate | |
TiN | Ti[N(CH3)2]4 [ tetrakis(dimethylamino)titanium ] | Barrier layer, metal grille, etc. | |
Ti | TiCl4 (titanium chloride) | ||
Ta/TaN | |||
Au/Al/Cu | Metal layers, metal grids, etc. |
Extended Reading.
- Micro and Nano Processing | Overview
- Micro and Nano Processing | Photolithography - Nanoimprint Lithography
- Micro and Nano Processing | Lithography - Focus on Ion Beam FIB
- Micro and Nano Processing | Lithography - Electron Beam Lithography
- Micro and Nano Processing | Photolithography - Optical Lithography
- Micro and Nano Processing | Etching
- Micro- and Nanofabrication | Thin Film Preparation - Epitaxy
- Micro and Nano Processing | Thin Film Preparation - PVD
- Micro and Nano Processing | Thin Film Preparation - CVD
We offer fast Thin Film Deposition / Micro and Nanostructure Processing Design Services, Feel free to leave a message to inquire.