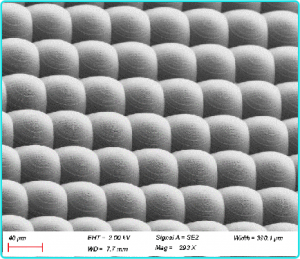
Micro and Nano Processing | MEMS Fine Processing (V)
1.5 High energy beam etching technology
(1 ) Electron beam etching
The chemical effect of the electron beam is used for etching. The surface of the workpiece is irradiated with a low power density electron beam, which hardly causes surface temperature rise, and when the incident electrons collide with the molecules of the polymer material, it causes the molecular chains to break or re-polymerize, thus causing the chemical properties and molecular weight of the polymer material to change, and using this effect, electron beam exposure can be performed. Exposure is mainly divided into two types, one is the electron beam scanning type, will be focused within 1 μm electron beam in the range of about 0.5 ~ 5 mm scanning, can be exposed to any graphics; the other is to reduce the projection type electron beam exposure, so that the electron beam first through the mask plate, and then to 1/5 ~ 1/10 of the proportion of the reduced, projected onto the electronic resist for large-scale integrated circuit graphics exposure. Electron beam etching is currently the best high-resolution graphics production technology, in laboratory conditions, up to 2 nm feature size, in production, generally can also reach 0.5 ~ 1 μm feature size.
Electron beam processing is carried out under vacuum conditions. In a vacuum environment, electrons can move at high speed, the cathode does not oxidize, and vapor oxidation of the processed surface can be avoided. Since the process is carried out in a vacuum, there are some limitations.
(2) Ion beam etching
Ion beam etching is a method that uses ions of inert gas elements or other elements accelerated into a high-speed ion beam stream in an electric field to perform various microfabrication processes with its kinetic energy, which is a promising method for processing with submicron or even milli-micron precision and a wide range of process capabilities. It can be divided into:
①Removal processing. First of all, argon, krypton or xenon and other inert gases into a low vacuum ionization chamber, with high-frequency discharge or DC discharge to make it equal ionization (i.e., the number of positive ions and negative ions equal mixture), in the role of accelerating electrodes, ions from the plasma is pulled out in a beam, from the surface of the workpiece to hit the atoms or molecules, so that you can directly complete the workpiece processing surface or graphics etching. Ion milling, ion polishing, ion thinning and ion sputtering all use this principle.
②Coating process. The microfabrication process of attaching low-energy incident ions to the surface of a workpiece is called ion attachment processing. A typical ion adhesion process is ion coating. In ion coating, the atoms or molecules impacted by the ion beam adhere to the surface of the workpiece with great energy, resulting in high coating strength and good coating quality. The ion-coating technology can be used to produce wear-resistant, corrosion-resistant, and heat-resistant surface strengthening films, as well as thin films for electronics, semiconductors, and integrated circuits.
(iii) Injection processing. Ion injection is to accelerate ions to tens to hundreds of kiloelectron volts (keV) energy, bombard the surface of the workpiece, the workpiece surface layer of high-speed ions into the atomic gap or in the form of replacement atoms embedded in the workpiece surface layer and retained in the surface process. In the production of integrated circuits, ion implantation can control the amount of doping and obtain uniform electrical parameters of integrated circuits.
④Ion beam writing map. Unlike electron beam exposure, electron beam exposure, the main factor affecting the resolution is the sensitivity of the photographic gel, the generation of secondary electrons and reflected electrons from the substrate, while the mass of ions is much larger than the electrons, scattering in the solid small, weak backscattering effect on the substrate, causing a small proximity effect, so can produce a line width of less than 0.1μm precision microfine graphics. Because the ion mass is large, the particle is large, the resistance to enter the resist is also large, so the range is short, so the ion energy is fully absorbed by the resist, so that the sensitivity of the resist increases.
(3) Plasma etching
Ion beam etching is a physical-based etching process. Plasma etching is a chemical reaction-based etching process. In plasma etching, low-temperature plasma is used, in which the chemical nature of the free radical is very active, and the chemical reaction with the etched material is used to etch the thin film material.
(4) Laser etching
Laser etching mainly uses solid-state lasers, and CO2 lasers have long wavelengths, which are generally not suitable for microfabrication. Theoretically, the diameter of the laser spot can be focused to 1 μm, but now the laser work material, due to the uneven quality of the material and the internal temperature distribution and other factors, the formation of the laser is prone to multiple oscillations or eccentric oscillations, so that the laser divergence angle increases, it is difficult to focus to about 1 μm. However, due to the intensity distribution on the focal plane, there is a narrow energy concentration band, so that there is a threshold of energy density that can be used for processing, so it can be processed than the spot diameter of the hole. The hole diameter of laser drilling can be as small as about 10 μm, with a depth-to-diameter ratio of 5 or more.
The main factors affecting the accuracy of laser etching are the effect of output power and pulse width; the effect of focal length and divergence angle; the effect of focal point position;The effect of energy distribution within the spot; the effect of multiple laser irradiation and the effect of workpiece material, etc.
We offer fastMEMS device / micro and nanostructure processing design services, Feel free to leave a message to inquire.
Related Products
Related Reading
Micro and Nano Processing丨Electron Beam Lithography (EBL) Technology Introduction
Micro and Nano Processing丨Electron Beam Lithography (EBL) Technology Introduction Contents What
Micro-Nano Processing | Introduction to Electroplating Process
Micro-Nano Processing | Introduction to Electroplating Electroplating is the use of electrolytic principle to make gold
Micro and Nano Processing | MEMS Fine Processing (III)
Micro and Nano Processing | MEMS Fine Processing (III) MEMS-oriented